Experimental Evaluation of Manufactured 2D Lattice Structures
This project is led by Dr. Josh Hamel with the assistance from the ME Lab Manager, Mau Gutierrez.
Research Problem
This project was concerned with the performance variations inherent in mechanical components produced using the same base material but via different digital manufacturing processes. Both CNC machines and 3D printers are digital manufacturing processes that allow for engineers to fabricate parts that have a great deal of geometric complexity with high degree of accuracy, but there is limited research available that analyzes similar parts produced via these two common manufacturing processes systematically. To fill this research gap, this project focused on the manufacturing of two-dimensional (2D) lattice structures, and then analyzing the test specimens for dimensional accuracy, the cost of manufacture, and mechanical performance in relationship to what is predicted in the literature.
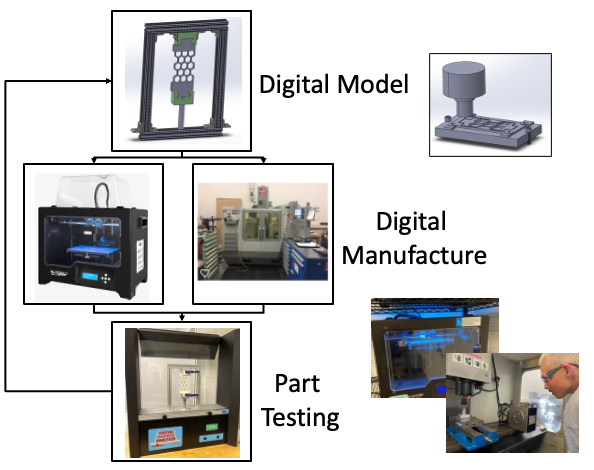
Fig: Experimental process to test the 2D lattice structure.

Microalgae Processing Research
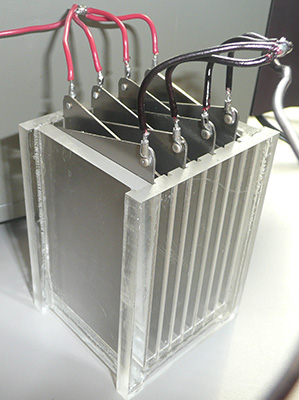
Several undergraduate students contributed to this research through design and testing of several microalgae processing devices. Their work was published in leading journals and presented at several Algae Biomass Summits, the largest algae conference in the US. The research effort is led by Dr. Shuman.
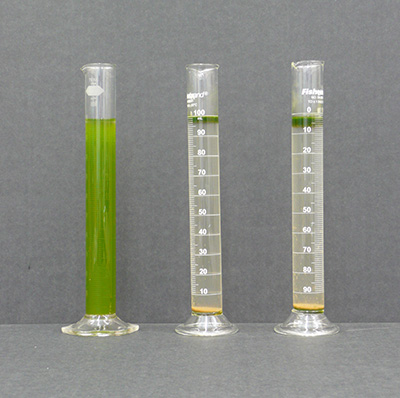
Recent Publications (undergraduate students underlined)
Journals:
- Shuman, T. R., Mason, G., Reeve, D., Schacht, A., Goodrich, A., Napan, K., and Quinn, J. “Low-Energy Input Continuous Flow Rapid Pre-Concentration of Microalgae through Electro-Coagulation-Flocculation” Chemical Engineering Journal, Volume 297, 2016, Pages 97-105
- Shuman, T. Rutar, Mason, G., Marsolek, M., Lin, Y., Reeve, D., and Schacht, A. “An Ultra-Low Energy Method for Rapidly Pre-Concentrating Microalgae” Bioresource Technology, Volume 158, April 2014, Pages 217-224
Conferences:
- Teodora Rutar Shuman, Ben Loveless, Jeremy Bjelajac, and Peter Griff “Continuous-flow Electro-Coagulation-Flocculation for rapid and ultra-low energy pre-concentration of microalgae”, 2017 Algal Biomass Summit, Salt Lake City, UT, October 29 - November 1, 2017.
- Teodora Rutar Shuman, Anthony Rock, Ben Loveless, and Jeremy Bjelajac, “Continuous-flow method for pre-concentrating microalgae with flow rates up to 5 L/min and energy inputs as low as 0.05 kWh/m3 of processed algal slurry”, 2016 Algal Biomass Summit, Phoenix, AZ, October 25th, 2016.
- Rutar Shuman, T., and Mason, G., “Rapid and Ultra-low Energy-use Pre-Concentrating of Microalgae” 2014 Algae Biomass Summit, San Diego, CA, September 29-October 2, 2014
- Rutar Shuman, T., Lin, Y., Bowman, C., Kurtz, V., Pawlak, G. D., “Microalgal Cell Vitality After Ultra-Low Energy Input Rapid Dewatering Process” 2012 Algae Biomass Summit, Denver, CO, September 24-27, 2012

Soft Robotics for Finger Rehabilitation
This project is led by Dr. Yen-Lin Han.
Motivation
- According to the 2018 US National Health Interview Survey conducted by the Centers for Disease Control and Prevention (CDC), 61 million adults in the United States have a disability where nearly 14% suffer from mobility.
- Current physical medical rehabilitation devices are expensive, limited, and more difficult to operate.
Goals
- Contribute to the advancement of wearable soft-robotic devices as a form of physical rehabilitation.
- Develop and fabricate untethered, light, flexible, portable, and affordable rehabilitation medical devices from soft polymers, gels, and fluids for easy at-home use.
Approach
- Investigate the use of a pneumatic or fluidic chamber-based actuator for finger rehabilitation.
- Experiment with phase-changing material (PCM) embedded elastomer soft robots that rely on the expansion of their soft structure due to fluid pressurization from thermal stimulus.
- Optimize the design of our prototypes, including actuation speed and reaction time, and required temperatures of PCM vaporization and pressurization for actuation.
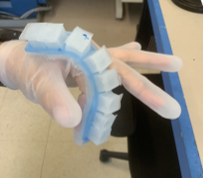
Fig: Image of an assembled PCM embedded soft robot for finger rehabilitation (not actuated)
Selected publications (undergraduate student’s name underlined):
- M. Cabrera, J. Van Liew, N. Turoski, M. Baysa, Y.-L. Han, “Utilizing Computer Modeling to Develop a Wearable Soft Robot for Finger Rehabilitation”, 6th IEEE-RAS International Conference on Soft Robotics (RobSoft 2023), under review.
- Baysa, M., Cabrera, M., Turoski, N., Han, Y.-L., ““Extensor” Soft Robot for Clenched Fist Rehabilitation After Stroke”, Design of Medical Devices conference, 2023, under review.
- Glasgo, N., Soohoo, M, Han, Y.L. (2022) Investigating the Design of a Soft Robot for Finger Rehabilitation, 2022 ASME International Mechanical Engineering Congress and Exposition, Columbus, OH: ASME.
- Taylor, M., Westra, K., & Han, Y.-L. (2020). Developing a Thermally Actuated Soft Robot for Finger Rehabilitation. 2020 ASME International Mechanical Engineering Congress and Exposition, Virtual, Online: ASME. https://doi.org/10.1115/IMECE2020-23134.

Composite Material Mechanics & Actuation Laboratory
What is Past is Prologue. Dr. Frank J. Shih leads this research laboratory working with undergraduate students. In the past few years, the lab group explored numerous combinations of material design and manufacturing parameters to develop novel composite material systems suitable for various applications of interest. These applications include improving impact energy absorption characteristics, interlaminar strength improvement, large-scale physical actuation, and improving thermal conduction. The laboratory's mission is in its membership - to foster the growth of undergraduate student engineers and scientists, such that they grow their capabilities, potential, breadth, taste, vision, and experiences in an enjoyable and positive environment. The lab's motto is "Who do you think you are? One contributes what one can!" as S. Timoshenko (1878-1972) told J. P. Den Hartog (1901-1989), according to Yuan-Cheng Bert Fung (1919-2019).
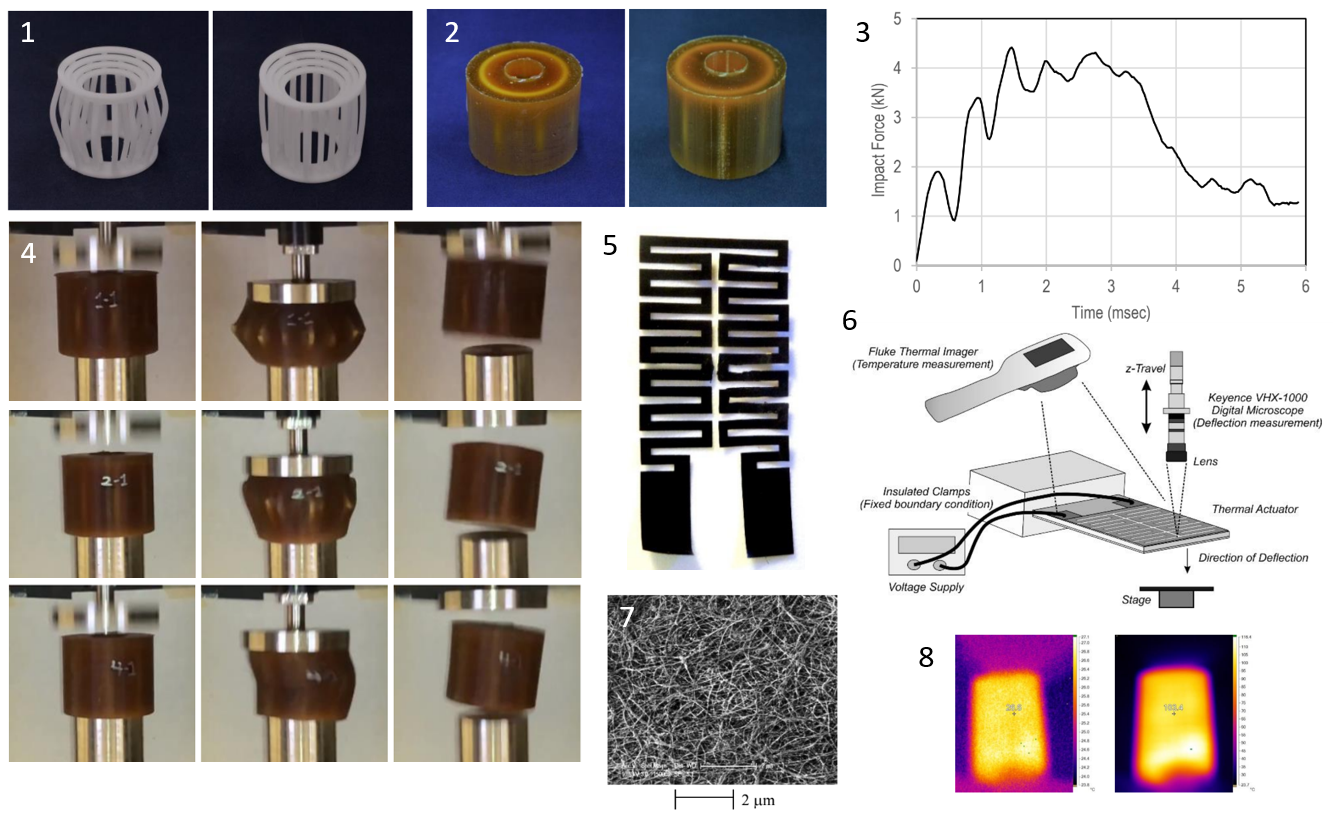
Fig: Some experiment images from recent efforts: (1) SLA printed nested curve beams, (2) encapsulated in elastomers, (3) impact force-time plot 4-kN in 6-ms, (4) impact tests sequence screen capture, (5) fabricated carbon nanotube sheet film resistor, (6) actuation deflection measurement setup, (7) photomicrograph of CNT sheet, (8) thermal imaging during actuation.
Selected publications & presentations (student's name underlined):
- Shih, FJ. & Chow, DJ, “Longitudinal Data-Informed Characterization of the Mechanical Engineering Profession for a Pre-College Student Audience,” Technical Presentation, ASME2022-99102, 2022 ASME IMECE, Columbus, OH: ASME
- Van Valkenburgh, OF, Ekstrom, TC, Goodman, EM, Leborte, CC, Haaland, KM, Yasuda, NK, & Shih, FJ. "Energy Absorption Characteristics of a Nested Curved Column Reinforced Elastomer Composite." Proc. of the ASME 2019 IMECE. https://doi.org/10.1115/IMECE2019-12096
- Traina, DJ, Ekstrom, TC, Van Valkenburgh, OF, Wallis, JR, Schulman, DS, Mather, ER, Yasuda, NK, & Shih, FJ. "A Three-Dimensional Nested Reinforcing Mesh in Elastomers for Crashworthy Applications." Proc. of the ASME 2018 IMECE. https://doi.org/10.1115/IMECE2018-88471
- Yasuda, NK, Schulman, DS, Traina, DJ, Mather, ER, Lane, KV, Lo, ME, Weaver, KD, & Shih, FJ. "Investigation of Energy Absorption Characteristic of Ceramic Fiber Reinforced Elastomer Composites." Proc. of the ASME 2017 IMECE. https://doi.org/10.1115/IMECE2017-72103
- Bever, AM, Brown, PJ, Lane, KV, Levy-Wendt, BL, Yasuda, NK, Han, Y, & Shih, FJ. "Characterization of a Fast-Responding Composite Thermal Bimorph Film Actuator Based on Carbon Nanotube Sheets." Proc. of the ASME 2015 IMECE. https://doi.org/10.1115/IMECE2015-52576

Screening and Optimization of Cryoprotective Agents (CPAs)
This project is led by Dr. Shen Ren.
Introduction
- Organ transplantation remains the most effective treatment for organ failure patients. However, there is severe organ shortage due to the lack of long-term organ preservation method. E.g., the current technology could maintain the viability of hearts and lungs for up to 4 hours, intestine, pancreas, and liver for 8 to 12 hours, and kidney for up to 36 hours.
- Cryopreservation is a promising long-term organ preservation method. To date, organs are able to be cooled down to storage temperature through vitrification, but rewarming requires more exploration.
- Investigation into which CPAs function well with Single-mode Electromagnetic Resonant Cavity is essential for the further development of this rewarming technology for organ preservation.
Experimental Design
Test Materials
- 10% - 60% Dimethyl Sulfoxide (DMSO), DPVP, 40D10G6P, VS55, 0.1M, 0.25M, and 0.5M Trehalose (+10% DMSO), 10% - 50% Propylene Glycol (PG).
Reference Materials for Calibration
- Water, Methanol, Ethanol, Ethylene Glycol, 1-Propanol, 2-Propanol, Cyclohexane.
.png)
Fig: CPA proposal and evaluation process.